Value chain activities
- Identify your product value chain
- Strategy & organisation
- Upstream supply chain
- Own manufacturing
- AkzoNobel: Measurement and follow up of own operations
- AkzoNobel: Code of conduct
- AkzoNobel: Eco-efficiency assessment to evaluate production alternatives
- SCA: Olawa factory is powered by nature
- SCA: Environmental management system
- SCA: Resource management system (RMS)
- SCA: Occupational health and safety
- SCA: Chemical assessments
- Customers and consumers
- Develop more sustainable products
- End-of-life of products
- Other stakeholders
Navigation by keywords
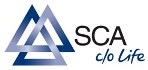
Environmental management systems at SCA facilities for personal care products
By Ann-Christin Pålsson & Ellen Riise
Environmental management systems according to ISO 14001 are implemented at SCA manufacturing facilities to secure structured and systematic work with environmental issues within the facilities. The work with implementing and maintaining the environmental management systems is run by each production facility.
All facilities for personal care products in Europe have a QRESH coordinator, with responsibility for coordinating issues relating to Quality, Risk, Environment, Safety and Health within the facility. The QRESH coordinators participate in a network to facilitate harmonisation of work between facilities. When needed for common issues or specific questions, the work is also supported by the central environmental department.
Specific measurement and follow-up for the environmental work is organised in the respective facility, supported by specific information systems. Information is also reported through the SCA group Resource management system (RMS). Further information about RMS is available here.