Value chain activities
- Identify your product value chain
- Strategy & organisation
- Upstream supply chain
- Own manufacturing
- AkzoNobel: Measurement and follow up of own operations
- AkzoNobel: Code of conduct
- AkzoNobel: Eco-efficiency assessment to evaluate production alternatives
- SCA: Olawa factory is powered by nature
- SCA: Environmental management system
- SCA: Resource management system (RMS)
- SCA: Occupational health and safety
- SCA: Chemical assessments
- Customers and consumers
- Develop more sustainable products
- End-of-life of products
- Other stakeholders
Navigation by keywords
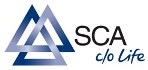
Occupational health and safety in the SCA hygiene business
By Ann-Christin Pålsson & Ellen Riise
The work with occupational health and safety issues for the SCA hygiene business includes procedures for hazard and risk assessment of chemicals and materials that are introduced within process development and at the manufacturing facilities. For chemical products, a specific chemical assessment is performed and if there are specific concerns, also a toxicology assessment is performed, see SCA: Chemical assessments
In addition to assessments that are performed for occupational health and safety, detailed product safety assessments are performed for all materials that is included in the product. This is further described in the activity for “developing more sustainable products” at this site.
Hazard assessment
The occupational health and safety assessment is initiated when introducing a new material. Based on available information about the material from the supplier e.g. Safety data sheets, and how the material is to be used, a hazard assessment is performed and reported. A material can be approved, sometimes under certain conditions or restrictions, or not approved with the reasons for this, e.g. chemicals on SCA’s restricted list or lack of information.
Risk assessment
A risk assessment is made on every material that is used. The basis for this assessment is the hazard assessment, together with the internal working procedures for how materials are handled. In addition, relevant legislation is used.
The purpose of the risk assessment is to secure occupational health and safety and to define necessary actions to ensure that these requirements are met.
A standard template is used for evaluation of risk, according to specified criteria. The assessment is performed by competent personnel in the workplace where the material is used. Based on the assessment, actions are defined and implemented to ensure that the risk is minimized. The procedures is implemented in the quality management system.